JXQ800 Diamond Wire Slicing System
Introduction
JXQ800 diamond wire slicing machine is mainly used in energy industry for slicing of mono-crystal silicon rods and poly-crystalline silicon rods. This diamond wire slicing system can realize the rapid cutting of silicon, reduced loss of cutting chips, silicon recycling, silicon surface consistency, and so on. The JXQ800 diamond wire slicing machine developed by us enjoys stable cutting rate and high processing performance.
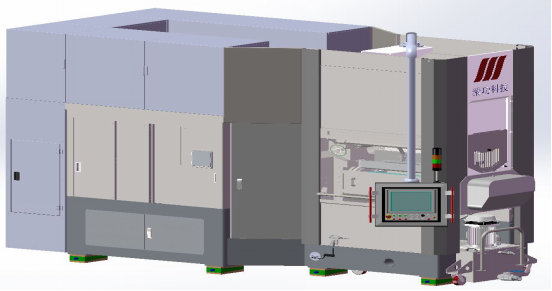
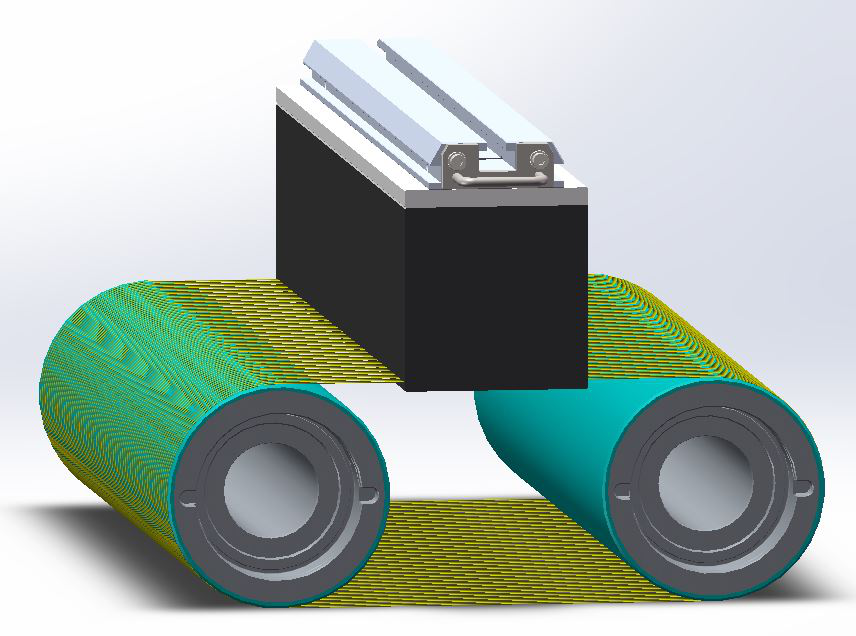
Technical Parameter
Model | JXQ800 diamond wire slicing machine |
Cutting size | 156 × L750mm |
Cutting head feed speed | 0 ~ 2mm/min (variable input control) |
Cutting head feed stroke | 285mm (max. 305mm) |
Silicon block clamping mode | Pneumatic |
Cutting time | About 2.5h (poly) / 1.5h (mono) |
Pay-off wheel specification | Φ366 × 140 |
Steel wire diameter | 0.06 ~ 0.08mm |
Wire speed | Max. 30m/s |
Steel wire acceleration | Max. 8m/s2 |
Steel wire tension | 5 ~ 25N |
Wire mode | Reciprocating |
Main roll distance | 370mm |
Main roll diameter | 190mm |
Main roll bearing box | Internal circulation, water cooling |
Cutting fluid temperature at nozzle | 16 ~ 22°C |
Cutting fluid supply | Max. 200kg/min |
Cutting tank capacity | 250L |
Cutting fluid cooling (plate heat exchanger ) | 50kW |
Cooling water pressure | 0.25 ~ 0.45MPa |
Water pressure difference | ≥0.15 MPa |
Cooling water flow | 10m3/h |
Average gas consumption | ≈15Nm3/h |
Intake pressure | 0.4 ~ 0.6MPa |
Power | 120kW |
Dimensions (L × W × H) | 4150 × 1950 × 3200mm |
Weight | About 14T |
Power supply | 50Hz, 3P, 380V AC |
Protection level | IP54 |
Mechanical Structure
Dimensions and composition
Frame
In order to prevent rust, the contact parts between the frame and the cutting liquid are made of stainless steel, which is solid and durable. The stainless steel door must be kept closed while the equipment is working to prevent damage caused by spatter of cutting fluid or other objects.
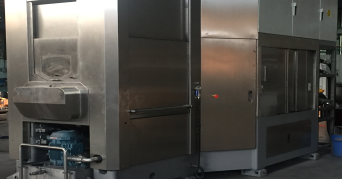
Winding management module
Wire winding management is an important part of the whole machine. It provides new steel wire to the cutting area, and finally rewinds the worn steel wire after cutting.
The main components include pay-off reel, cable pay-off, pay-off tension arm, take-up reel, cable take-up and take-up tension arm. The pay-off reel and take-up reel are all driven by the servo motor, and the tension is driven by the tension motor.
Cutting room
Cutting room is directly related to cutting. It consists of cutting head stand, table, guiding wheel, front and rear bearing box, wire mesh, mortar nozzle, broken wire detector and other components. Most of its interior parts are made of stainless steel, while some areas are protected (sealant, labyrinth structure, gas seal, etc.) to prevent the infiltration of cutting fluid, silica fume, etc.
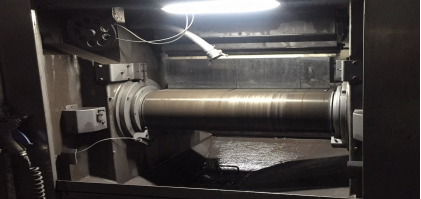
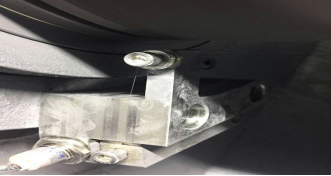
The guiding wheel has polyurethane coating with slot distance depending upon the cutting thickness. The water inside flows through the rear bearing box, the guiding wheel and the front bearing box, in this way, the internal temperature is kept constant and the influence on the cutting is reduced.
The broken wire detector uses proximity switches to quickly shut down the diamond wire slicing system after disconnection to reduce losses.
Cutting fluid loop
The cutting fluid loop controls and adjusts the cutting fluid parameter, such as flow, temperature, and so on. It consists of cutting liquid cylinder, plate heat exchanger, flow meter, filter and cutting fluid wires. The cutting fluid in the cylinder is pumped into the circuit by the cutting liquid pump. After filtering the silicon powder in the cutting fluid through the filter, the cutting fluid is cooled through the plate heat exchanger and then passes through the flow meter. After that, through the cutting liquid nozzle with stable flow and temperature, it flows into the cutting chamber, finally back into the cutting cylinder. The temperature of the cutting fluid is controlled by the plate heat exchanger. The general process requires the temperature of the cutting fluid controlled within 20°C.
The cutting liquid circuit adopts the shortest path, which effectively reduces the residue of sludge caused by long path. Using high-power plate heat exchanger can remove the heat produced when slicing.

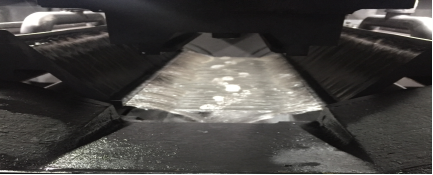
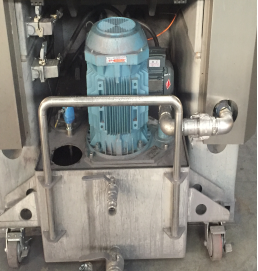
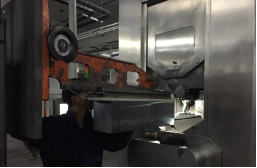
Multi-purpose car
Multi-purpose special car can not only load and unload silicon ingot, but disassemble wire wheel. This car is easy to operate and requires reduced labor intensity, thus improving work efficiency.
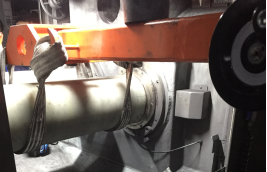
Electronic control system
Electric control system adopts SIEMENS SIMOTION motion controller, high-end SIEMENS servo actuator, other low-voltage electrical appliances from ABB and other high-end brands to ensure the reliability and precision of cutting. The man-machine interface of this diamond wire slicing machine provides friendly interface and allows simple operation. Despite monitoring the input parameter, this electronic control system can also record the historical operation data and diagnose fault, making it convenient for users to do data analysis and effectively monitor the operation status of the diamond wire slicing system. At the same time, the control system manages the authority of operation level, which can effectively prevent the operator from changing the operating parameter by mistake.
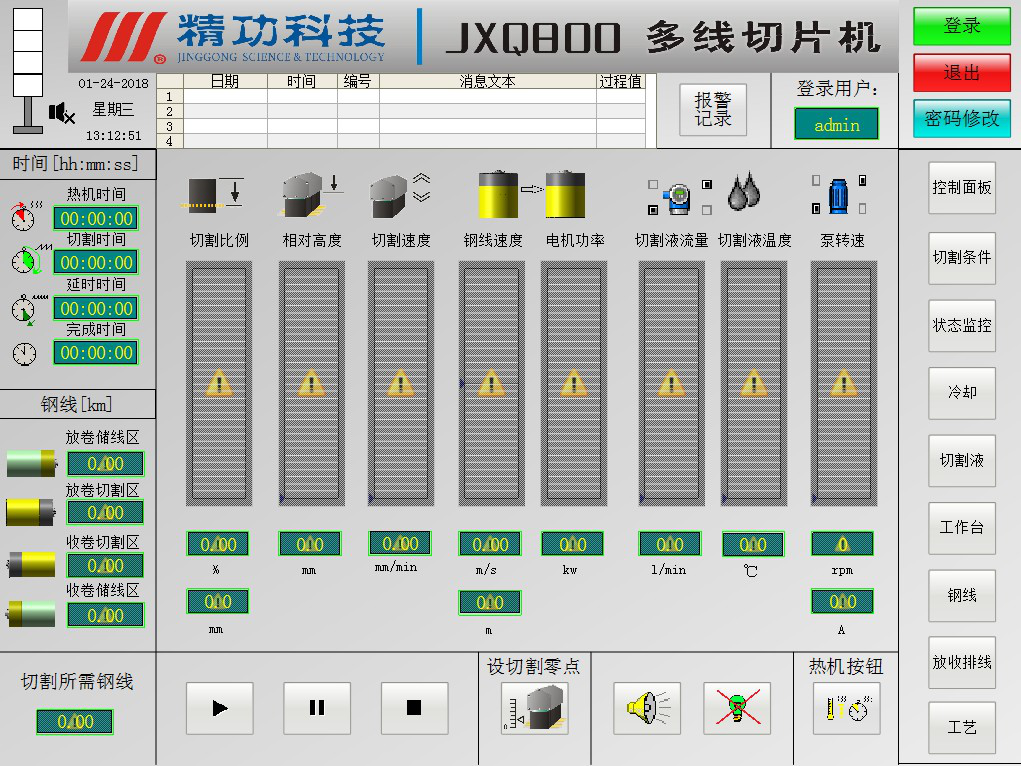
Main interface
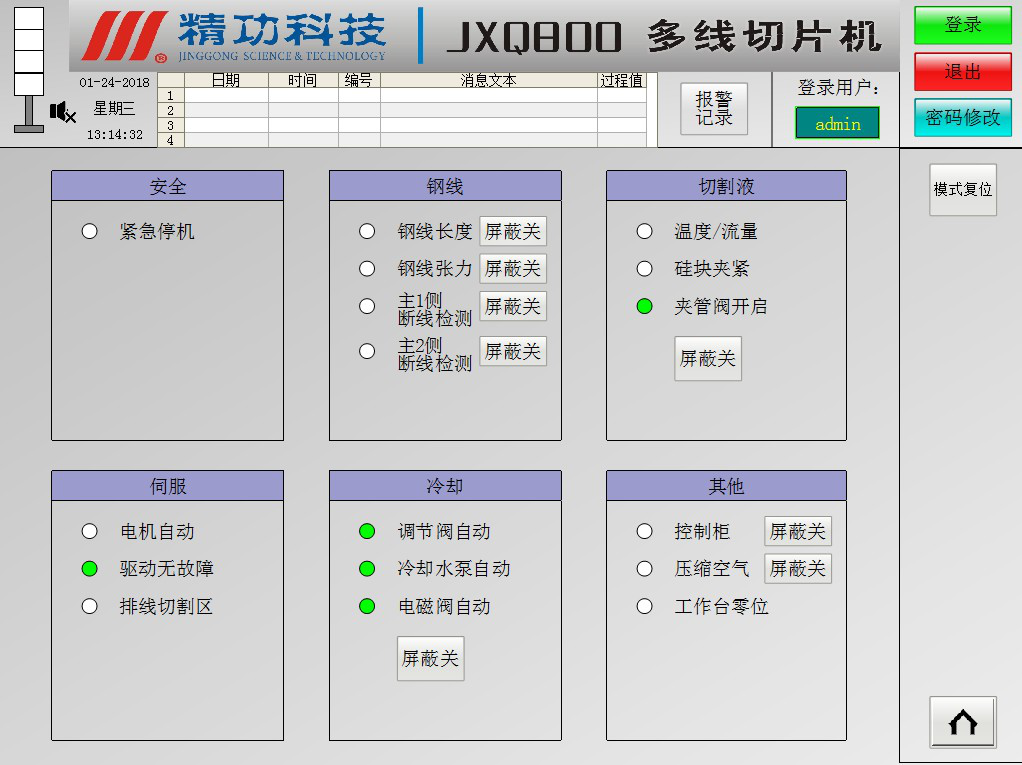
Cutting condition interface
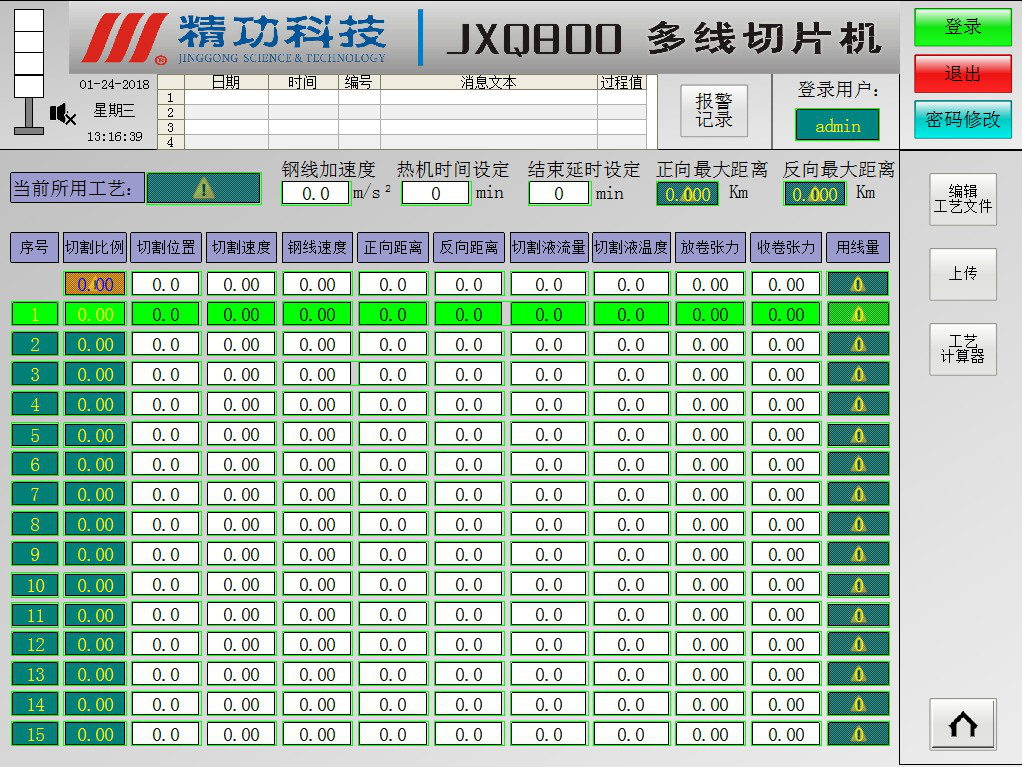
Cutting process interface
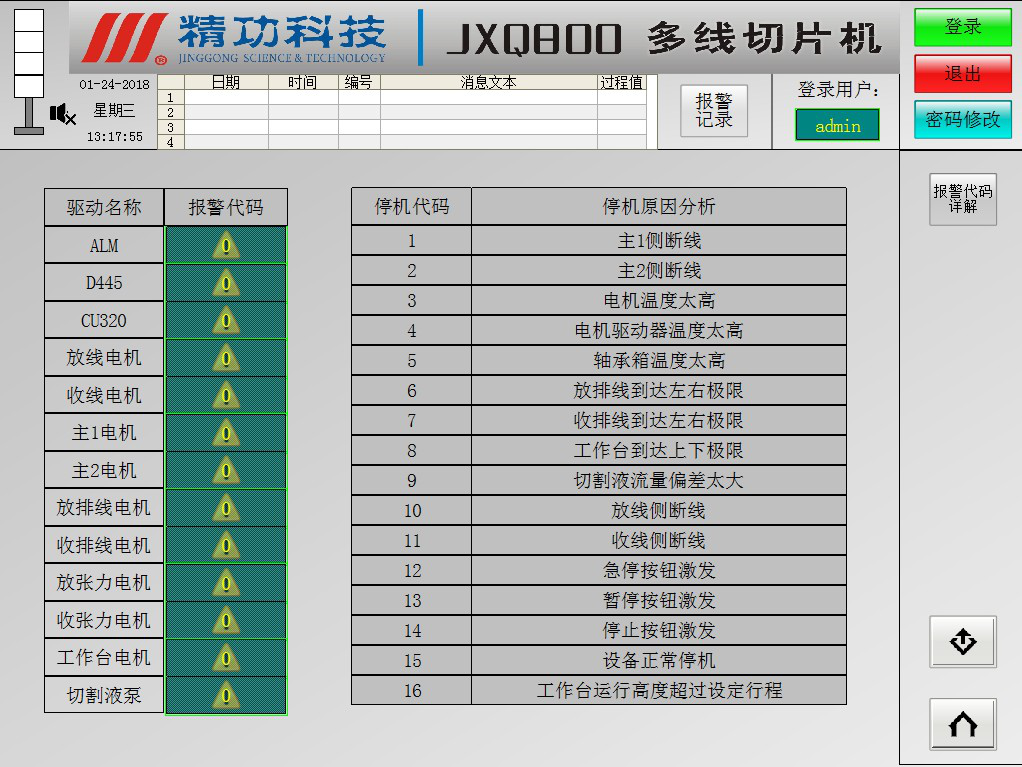
Diagnosis interface
Installation Requirements
-
Before installation and commissioning, customer has to meet the following requirements at its facility:
- 1. Foundation requirement
Concrete thickness: ≥300mm
Flatness: ≤±10mm/3m
Vibration requirement: no vibration - 2.Power requirement
Power: 120kW
Voltage: three-phase, 415±10%V AC, 50 Hz
Incoming wire: VV 3 × 120 + 1 × 50mm2 - 3.Environment
Humidity: <75% (no condensing)
Temperature: 23°C±5°C - 4. Cooling water
Water quality: no abrasive particles
Grain size: ≤0.1mm
Flow: 10m3/h
Pressure: 0.25MPa ~ 0.45MPa
Inlet and outlet pressure difference: ≥0.15MPa
Temperature: about 12°C - 5.Compressed air: provide dry, clean compressed air in accordance with DIN ISO8573-1
- 6.Inlet pressure: 0.4 ~ 0.6 MPa
- 7. Gas consumption: 60m3/h
Gas supply interface: φ16mm air pressure tube - 8. Lifting equipment: >14T